-
Clay Meets Robotics: Impact Printing for Eco-Friendly Construction
A new additive manufacturing technology dubbed impact printing uses excavated earth as a sustainable building material.
If we were to trace back to the earliest building materials used by humans, we would likely point to some type of vegetation or simple mud. It's no coincidence that adobe—unfired brick—was used in ancient civilizations such as Sumer and Egypt. Over time, more advanced materials like fired clay and concrete, along with sophisticated construction technologies like modular systems, were developed. Few would have predicted that a material as rudimentary as adobe would be paired with cutting-edge additive manufacturing technology.
However, this is precisely the breakthrough announced by ETH Zurich, which has found a way to use clay as a sustainable construction material. And no, it's not 3D printing as you might imagine.
Clay as a sustainable construction material
Clay is not only an eco-friendly and sustainable option but also one of the most abundant materials on Earth. This prompted ETH Zurich's research teams in Switzerland to explore whether it could be feasibly used in housing construction with the aid of technological innovation. Traditionally, structures made from clay have lacked durability and required significant manual labor.
Now, researchers at the Swiss institute have developed a groundbreaking technique involving a robotic system that forms clay or other excavated materials into projectiles, mixes them with silt, and launches them at high speed to build up walls vertically. Each ball of this sustainable material is propelled at a speed of 10 m/s.
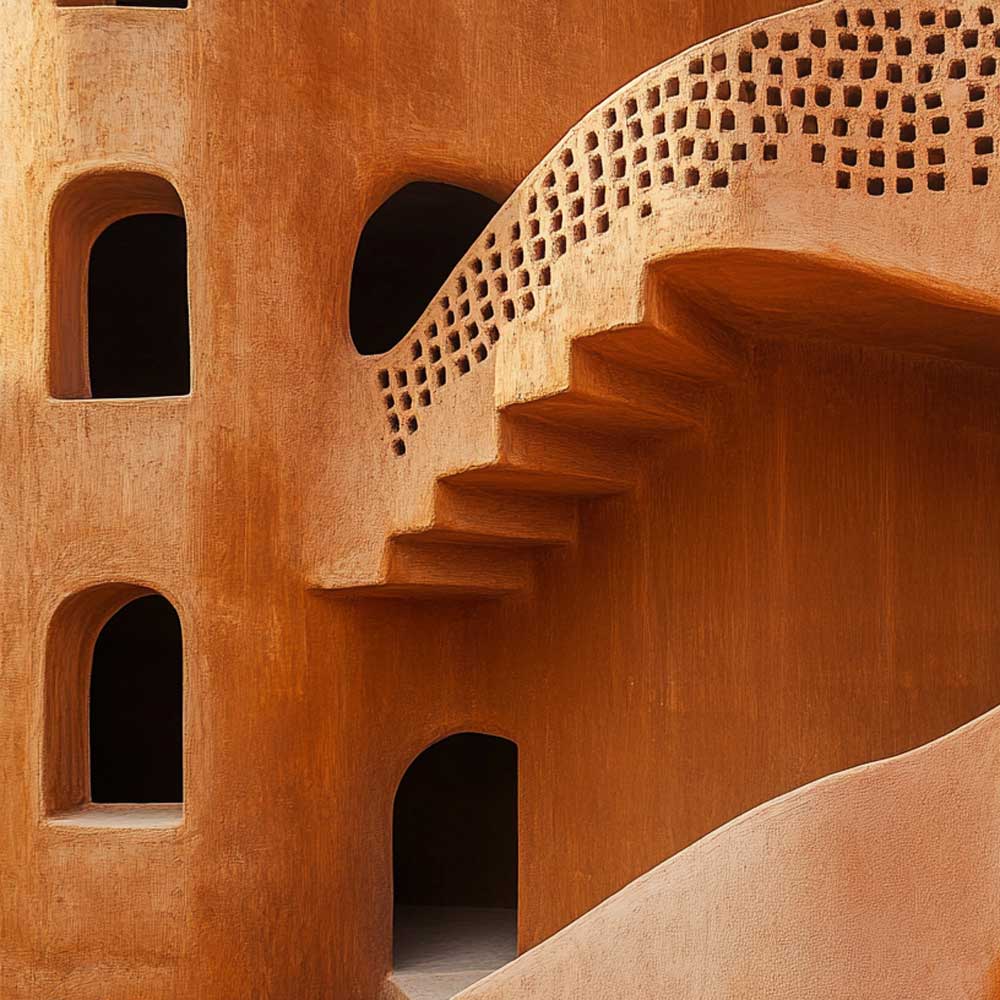
The project includes a portable machine, reminiscent of a 3D printer, that can be brought directly to construction sites to build walls on location. According to the project's leaders, the combination of traditional materials and robotics helps optimize production times and reduce costs.
A technology that leverages construction waste
The developers emphasize that only minimal use of additives is necessary for constructing robust structures. In initial tests, the team used a mix consisting of 75% construction waste blended with silt and other sustainable materials.
Unlike conventional systems where the material must set before adding new layers, this technique allows for clay to be applied continuously, even if the previous layer has not yet dried. This significantly accelerates the building process. The medium-term goal is to experiment with new mixtures to enhance results and broaden potential applications.
With this approach, ETH Zurich's system eliminates the need for concrete, reducing greenhouse gas emissions and the environmental impact typically associated with cement use. The basic robot is just the starting point; ongoing research is looking at robotic attachments to diversify the types of structures that can be built.
Watch the process in this video, showcasing impact printing in action as it constructs walls and columns:
Mycotecture: sustainable construction with fungi
Beyond natural materials like clay, other innovative disciplines are exploring the use of organic substances. One such area is mycotecture, which involves building structures and furniture using fungi. As previously covered in another article, this technique involves creating bricks by injecting fungal spores into a substrate. When these spores grow, they form a dense mycelium network. Growth is halted with heat treatment, resulting in “bricks” that can be used as thermal insulation and more.
To learn more about sustainable construction techniques and nature-inspired building materials, consider subscribing to our newsletter at the bottom of this page.
Source:
Image:
- Michael Lyrenmann / Gramazio Kohler Rese / ETH Zurich
Write your comment
All fields are mandatory.
Thank you for your comment
More about Construction
Featured topics
Read the most discussed articles
{{CommentsCount}} Comments
Currently no one has commented on the news.
Be the first to leave a comment.
{{firstLevelComment.Name}}
{{firstLevelComment.DaysAgo}} days ago
{{firstLevelComment.Text}}
Answer{{secondLevelComment.Name}}
{{secondLevelComment.DaysAgo}} days ago
{{secondLevelComment.Text}}